Testen und Entwickeln
Die letzte Woche stand unterm dem Motto „Testen und verbessern“. Der Weichenantrieb wurde auf Herz und Nieren geprüft. Auch wurde meine Zuggarage getestet. Alles in allem recht erfolgreich. Aber wie das immer so ist bei Prototypen, irgendwo hackelt es immer und man muss optimieren.Beim Weichenantrieb wurde der Arduino umgeschrieben, so dass er selbstständig hin und her schaltet. Wie das so bei Patienten ist, bekam der Antrieb gleich noch ein paar Kabel dazu, die seine „Fitalfunktionen“ ständig überprüfen sollen. Eigentlich wurde „nur“ die Taster angeschlossen und vom Arduino zusätzlich ausgewertet. Der Antrieb durfte dann selbstständig laufen. Anfangs wurde sein Zustand noch alle halbe Stunde überprüft, in dem eine Pfleger (ich) ständig in sein Zimmer gesprungen ist und ihn visuell inspiziert hat. Je länger der Test wurde je weniger habe ich mich um den Patienten gekümmert. Nach 38.000 Zyklen war ein „Softbreak“ eingebaut. Das war das mindeste, was der Antrieb erreichen musste. Nachdem gründlichen Prüfen wurde der Test wieder fortgesetzt. Ja, den 38.000 und 1ten Zyklus schaffte er nicht. Da brach die 0,5mm Federstahldraht. Doof gelaufen. Diesen dann durch einen 1mm Federstahldraht ersetzt und den Test wieder neu gestartet. Die 38.000 Zyklen waren diesmal dann keine Unterbrechung. Nach 4 Tagen war der Antrieb dann bei 200.000 Zyklen und wirkte zwar nicht mehr ganz so frisch wie bei seinem ersten Zyklus, aber noch Munter genug, um die nächste Härteprobe in Angriff zu nehmen: Ein Ausflug zu den Clubkolegen ins Vereinsheim. Dort musste er sich dann den prüfenden Augen der Kolegen stellen. Hat er auch wunderbar geschafft. Insgesamt hat er vor Ort nochmal 100 Zyklen aufgespielt bekommen. Insgesammt hat die Mechanik damit grob 240.000 Zyklen auf dem Buckel (die Differenz die man jetzt aus den Angaben im Text erschließt, kommt daher, dass zwischendrin auch noch Tests gemacht wurde, um ihn zumindest in den Anfängen auf den richtigen Weg zu bringen, welche aber nicht mit in die Zyklen gezählt haben, diese Kurztests wurde aber auch alle ohne Probleme überstanden).
Ein paar Bilder habe ich auch noch:
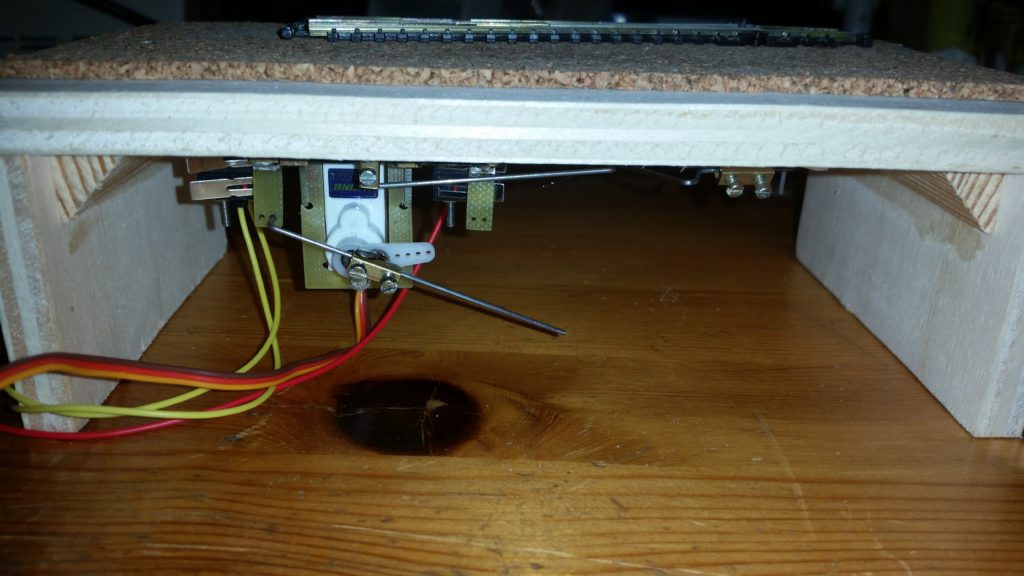


Das nächste war die Zuggarage. Ja, inzwischen hat diese einen Namen bekommen. Dort stand letzte Woche noch die fehlende Rampe aus. Inzwischen wurden mehre Prototypen im 3D-Druck Verfahren hergestellt. Der erste Prototyp wies noch erhebliche Mängel auf. Auch konnte ich ein paar Punkte wieder dazu lernen, die in der Konstruktion für 3D-Druck Teile wichtig sind. Überhängen kann man Drucken, sollten aber nicht mehr als 45° haben. Sonst verzieht es die Maße bis hin zur Unbrauchbarkeit (Feile und Schleifpapier sollten zwar immer parat liegen, aber in dem Fall waren sie schon stark im Einsatz). Mit dem ersten Prototypen wurden ein paar Funktionen getestet. Leider musste ich aber feststellen, dass manch ein Hersteller gerne noch Schneepflüge, Sanungsnalgen und Kupplungen einbaut. Kupplungen ist mir völlig rätselhaft, wozu diese gebraucht werden :-D. Jedenfalls konnte ich zwar mit dem Prototypen der Vorserie einige Erfahrungen sammeln, die ich dachte, dass ich im 2. Prototyp ausgebessert hatte. Schneeräumer und Kupplungen mögen die Rampe aber immernoch nicht. Inzwischen ist Version 3. im Test. Insgesammt wurde die Länge von 150mm und die Höhe von 10mm auf nun eine Länge von 350mm und eine Höhe von 15mm geändert. Die 15mm führten vermutlichim 2. Prototyp dazu, dass Schneeräumer und Kupplungen ärgerlich sind. Sollte nun durch eine Änderung der Länge ausgebessert sein (Die Länge beeinflusst die Steigung und damit auch den Winkel, den die Lok selber hat, bis sie auf der Rampe ist).
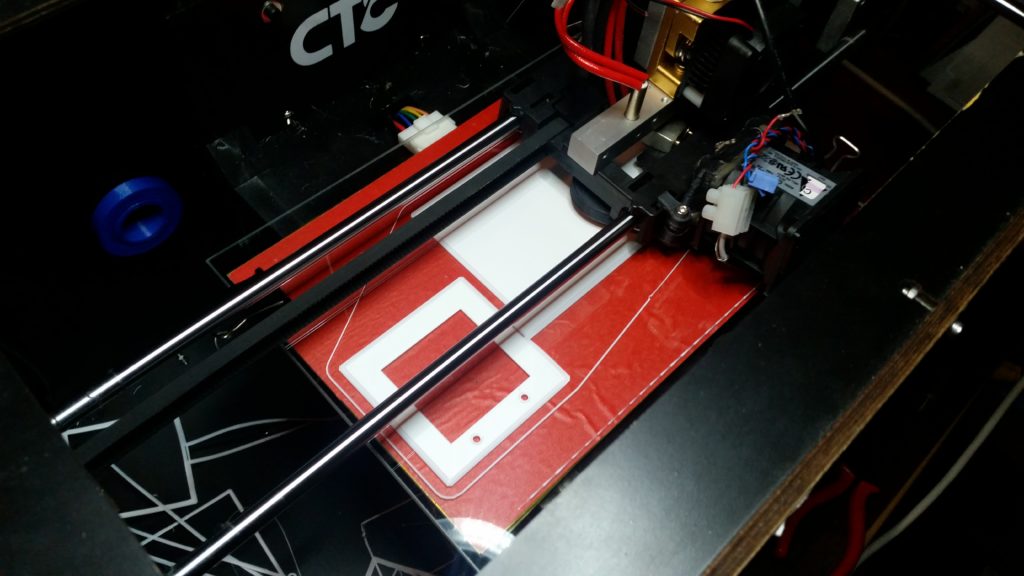
Vom ersten Prototyp gibt es wieder zahlreiche Bilder und auch ein Video:
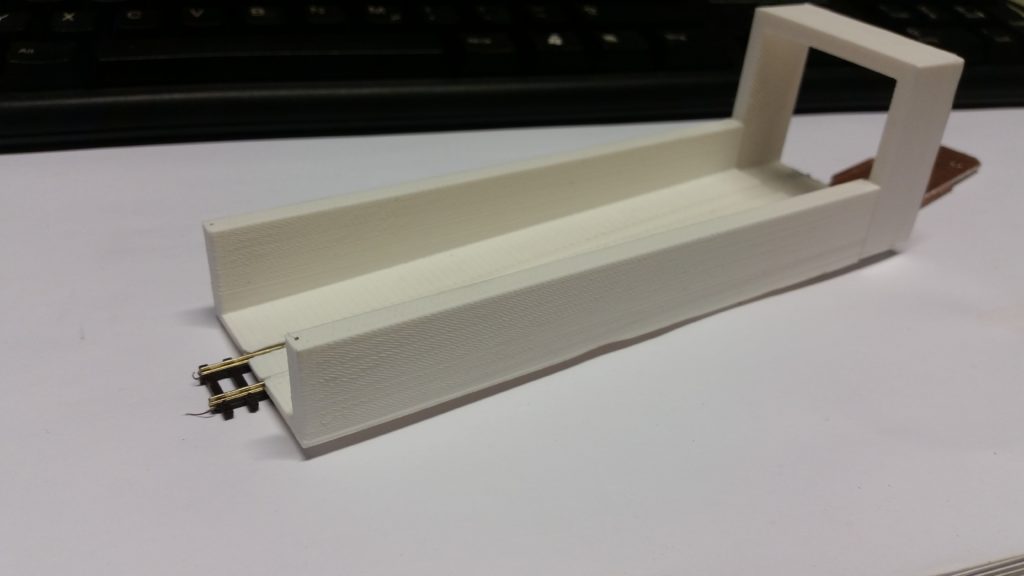
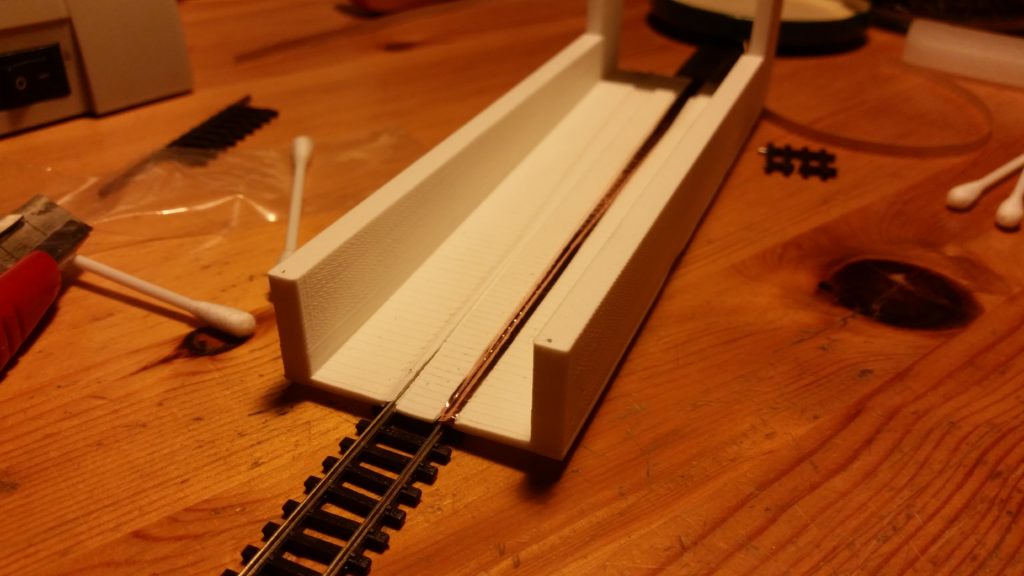
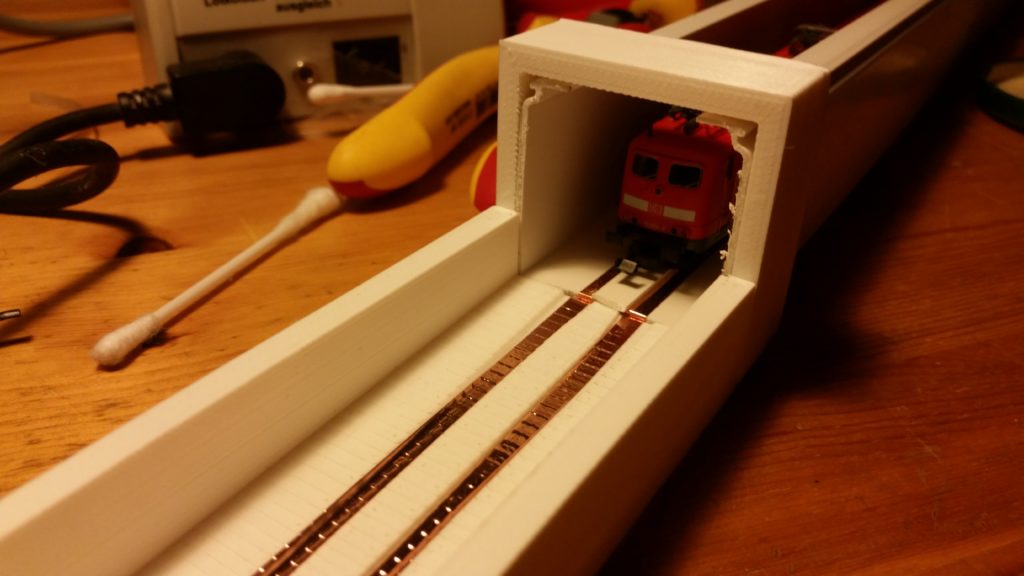
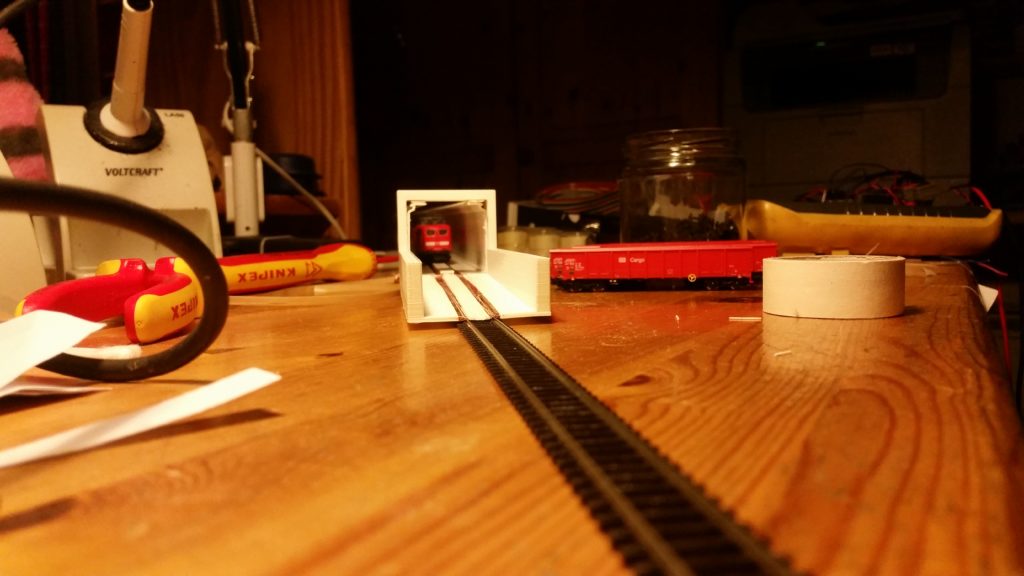
Und nun das Video dazu: